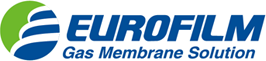
Hydrogen recovery in ammonia/methanol plant
Hydrogen is the main material for ammonia synthesis process. To keep the partial pressure of hydrogen in the synthesis tower in order to get the reasonable reaction rate, the synthesis loop must be purged continuously to avoid build-up of inert gases (e.g.: Ar+CH4+N2).
When the syngas is used to produce methanol, the synthesis loop must be also purged continuously to avoid build-up of inert gases (Ar+CH4+N2). These purge gas typically contains 60-80% H2.
Applications:
• Ammonia vent gas
• Methanol vent gas
• Syngas
Performance:
• H2 recovery: > 90%
• H2 purities: > 90 mol%
• CO purities: >95 mol%
• Control the ratio of H2/CO
Operating characteristic:
• Max. operating temperature: up to 90°C
• Max. operating pressure differential: up to 90 barg
Scope of supply:
• Pretreatment
• H2 Membrane unit
• PSA as post-treatment (upon request)
Standards:
• Pressure: ASME, BPVC VII Div1
• Electrical: IEC or NEC
• ISO 9001 certified process
• Hazardous (ATEX/Class Div2)
References:
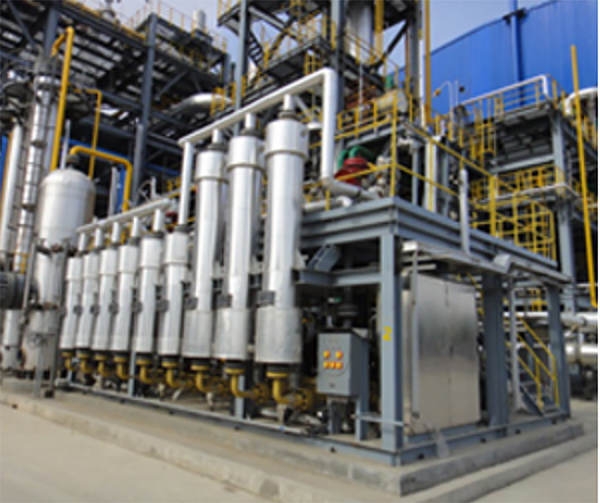
Location: China
End user: Petrochina
Application: 450 kta/year Ammonia
Capacity: 46,000 Nm3/h
Feed pressure: 14.4 MPaG
Design pressure: 17 MPaG
H2 recovery: ≥90%
H2 purities: ≥93 mol%
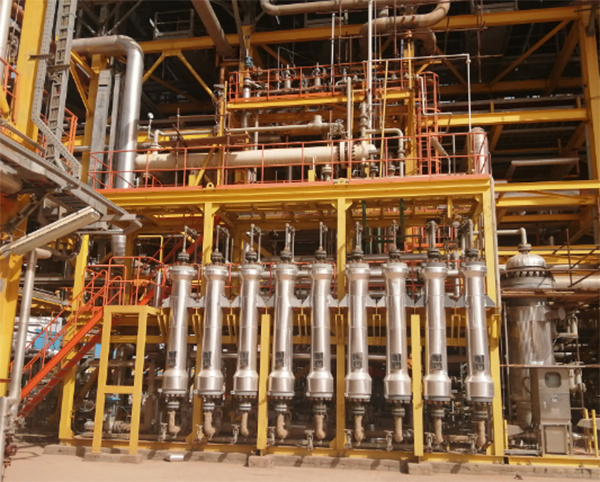
Location: Middle East
Application: 2,050 MTPD Ammonia
Capacity: 32,000 Nm3/h
Feed pressure: 12.0 MPaG
Design pressure: 14.0 MPaG
H2 recovery: ≥87.4%
H2 purities: ≥95 mol%
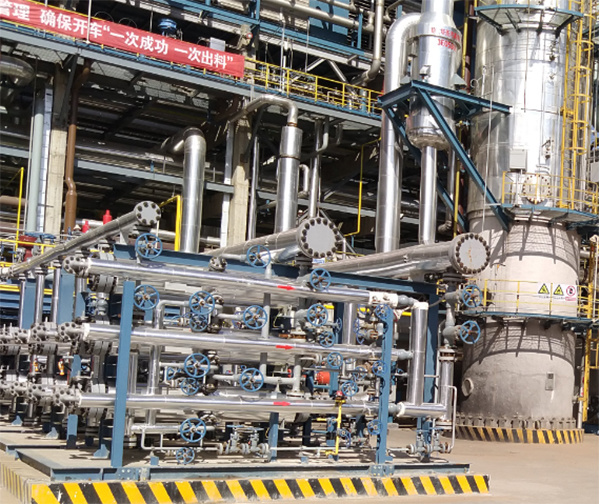
Location: China
End user: Chinacoal
Application: 1 Mt/y Methanol
Capacity: 120,000 Nm3/h
Feed pressure: 8.0 MPaG
Design pressure: 10.0 MPaG
H2 recovery: ≥85%